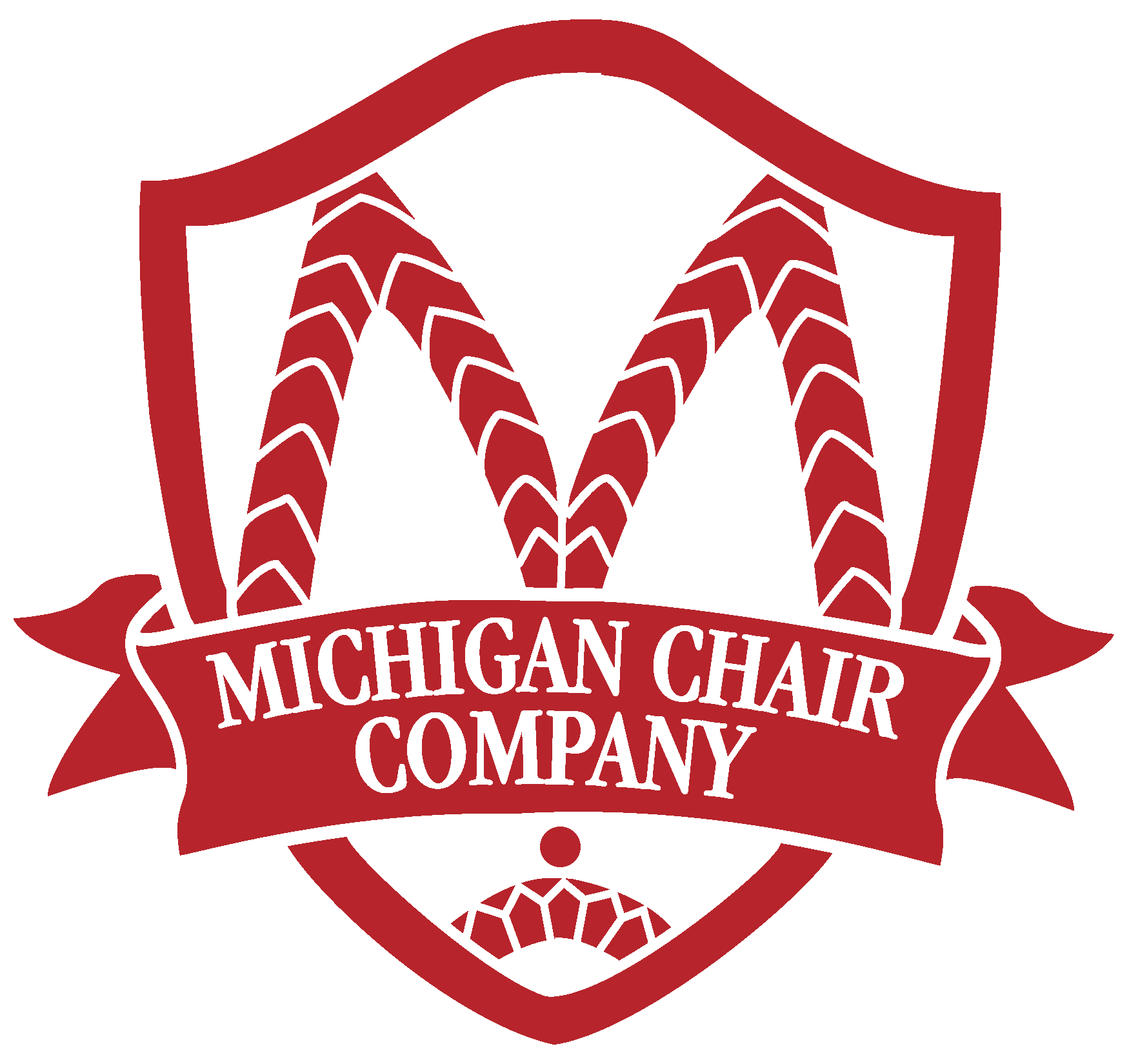
Michigan Chair Company
A solid hardwood steam bending company
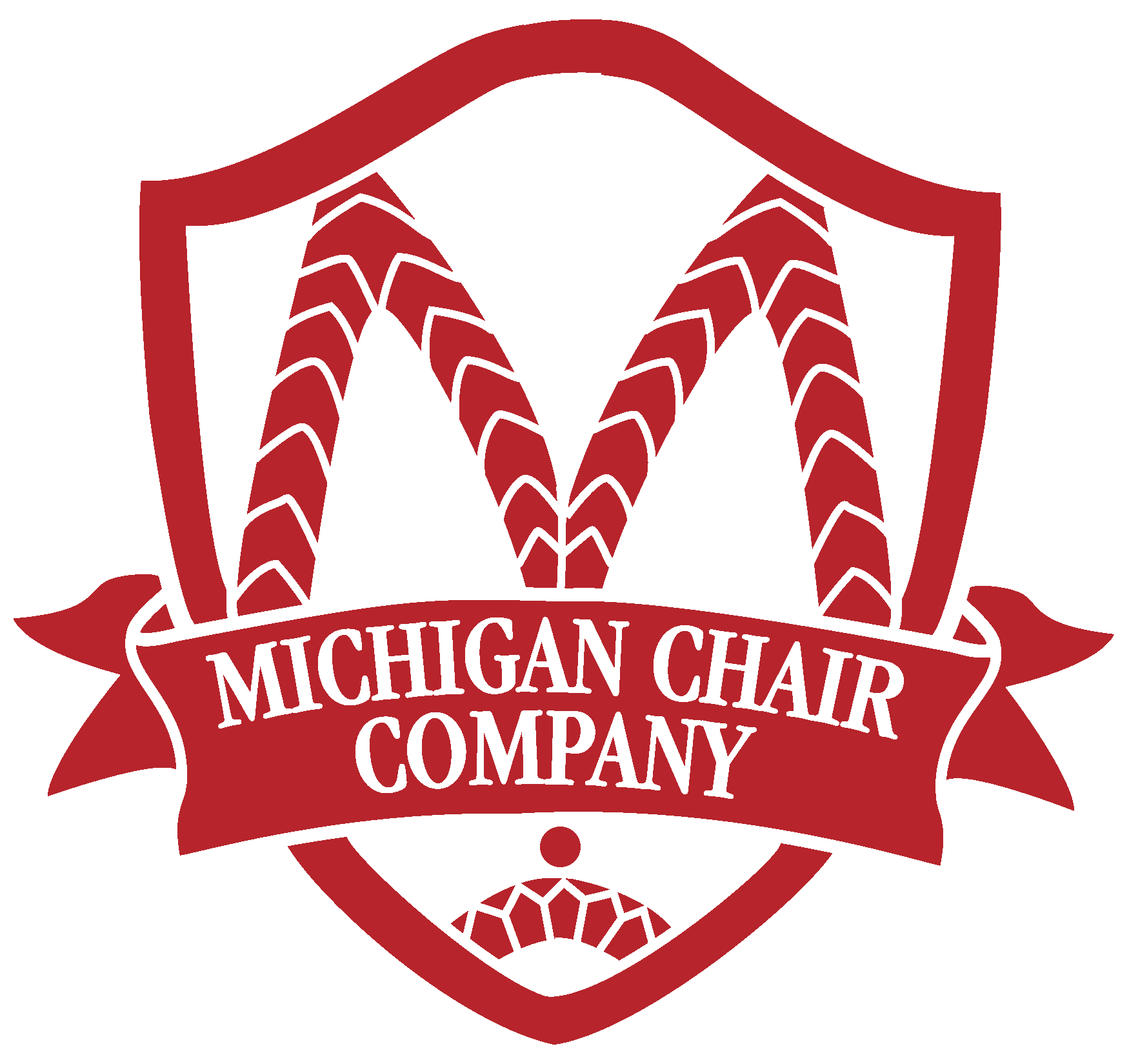
Michigan Chair Company is a custom solid hardwood steam bending company marketing to both residential and contract furniture manufacturers. Michigan Chair Company’s customers range from large multinational companies to single person studio furniture makers. Customer satisfaction is always a priority at Michigan Chair Company, and we strive to meet all of our customers’ needs and requirements. We specialize in high quality steam bending to your specifications with a fast turnaround time.
Value is a word that is bandied about by companies when selling anything from fast food to automobiles. What exactly are you getting for your money? Price, of course, is a key component of value, but quality and delivery are also part of the value equation. If you get promises of when the bendings will come in, but they do not show up until weeks later in turn making your company late, are you getting value? If the steam bendings come in not at the specified shape, or with high moisture content, are you getting value? Do you want your employees bending them into the exact shape so they can be machined? Are you prepared to deal with bends moving as they continue to dry out? We address these issues.
Michigan Chair has been bending since 1946. You have the assurance knowing that we deliver by an agreed upon due date. We dry bends to between 6-8% moisture content, and adjust the shape to match your specs before they are shipped. If you think that you have a problem that may be solved with steam bending, give us a call. We will give you an honest evaluation of how well bending will satisfy your expectations in comparison to similar products.
Michigan Chair is a business to business company.
Contents
1.1. Short grain strength problems
1.2. Upgrading your product line?
2.2. Circle geometry refresher
2.3.Clamming / Why do bends move
2.6. Bending taller than wide or bending the hard way
2.12. Why don’t most tropical species bend well?
3.1. Wood shrinkage comparison
3.4.1 Brown, orange, and gray stain in wood
4. Scientific and industry terms
4.1. Rift, Quarter, and Flat or Plain Sawn
4.3. Modulus of Rupture, Elasticity, and Compression
4.3.1. Are these numbers useful in predicting how well a species will steam bend?
4.5. What is difference between rift sawn, quarter sawn, and flat sawn lumber?
5.1.1. Selected species that bend well
5.1.1.4.2.1. What is the difference between hard, red, and silver maple?
5.1.2. Selected species that are difficult to dry without degrade
5.1.2.1.1. What is the difference between red and white oak?
5.1.3. Species that do not bend well
6. Environmental impact of using wood products
7. Economic impact of using wood products
11.1. Michigan Chair brand bends
11.3. 1924 Michigan Chair Catalog
11.4. 1926 Michigan Chair Catalog
11.5. 1930 Michigan Chair Catalog
Please contact either Tim or Bob for more information and a personalized quote today. (231) 937-4367
Michigan Chair Company is a proud member of the following industry organizations:
The benefits of steam bending
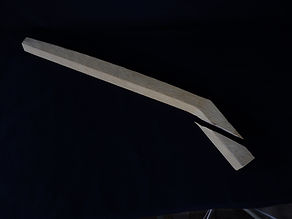
Short grain strength problems?
The arm, pictured above, was sawn perpendicular to the stem into the transverse or cross-sectional plane, and broke when a comparatively small force was applied as would occur when someone sat on the arm, or if the chair tipped over. If this happened with a back leg to a chair with a large splay, the results can be serious. These weaknesses are usually revealed during BIFMA, or other strength testing. Wood is strongest when sawn parallel to, but without passing through, the pith; this is the tangential plane. Wood sawn in a plane passing through the pith (as a radius of a circle) is labeled the radial plane or surface. Any time a saw deviates from the way the wood would split, the wood is weaker. This deviation is called the slope of the grain. The greater the slope, the weaker the wood will be. If your design specifies a curve in an arm or leg to a chair that has a large degree of slope, then there is the potential for the wood to fail. Steam bending solves these short grain issues because the long grain now follows the entire length of arm. If your chair would either fail, or did fail in testing, then steam bending is the first choice to solve the problem.
Upgrading your product line?
One way that high end furniture designs can distinguish themselves from commodity furniture is by reducing the number of joints and glue lines. When the long grain of the wood follows the curve, a premium look is achieved. Inexpensive wood furniture utilizes wood either from glued up panels of narrow boards, or from using short pieces with multiple end joints to make curves. A lacquer finish will eventually crack at the joints. Glued up panels can get a zebra striped look from the numerous changes of color often referred to as “flip”. Flip also occurs as either the radial or tangential planes change into the cross-sectional, or end grain. This is difficult to mask because the effect is largely due to the changing angle of light reflection. A steam bent rim will only show the tangential and radial surfaces of the wood.

Bending Terms
Dimension conventions
The meaning of width and thickness are relative to the context they are used in. We use the following dimension conventions without exception. Whenever we communicate with you, the dimensions are always in the following order, and refer to the orientation in the drawing to the right:
A x B x C
The length “A” is seldom misunderstood. In our shop, we refer to “B” as the width and “C” as the thickness. A table top manufacturer would usually refer to the “B” as the thickness, and “C” as the width.

Circle geometry
If it has been a while since you took geometry, and are unsure of the difference between radius and diameter we offer this diagram as a refresher. We need to determine the arc length on the outside of the bend; this arc length is the length of the bending blank that we start with. Four part construction refers to a bend that will cover ¼ of or 90° of a circle, it will take four pieces to completely edge band a table. Three part construction refers to a bend the will cover 1/3 or 120° of a circle, it only takes 3 parts to completely edge band a round table.

Clamming or how and why steam bendings move
When humidity levels fall, steam bendings will lose moisture and begin to shrink. Steam bending compresses the wood on the inside radius of the bend (there are more wood cells per cubic inch of wood than on the outside of the bend). The wood cells on the inside shrink more than the outside of the curve causing the ends to move closer together. Correspondingly, rising humidity is absorbed by wood cells causing the expanding cells to move further apart. Clamming is a bending term to describe this phenomenon.
Listed below are several relationships to help anticipate what may happen:
-
Wood will change moisture content more rapidly at higher temperatures.
-
Extreme dew points in the 70s and higher as well as those approaching 0 will induce a more rapid change. However, the time frame involved is usually at least a week.
-
Slow drying species will absorb water more slowly and change shape more slowly. Fast drying species will change more rapidly.
-
Smaller curves tend to move more than larger curves.
-
Very flat curves, as in 100 inch radii, tend just to flatten out.
-
Long curve lengths will move more than shorter lengths.
These effects can be offset by:
-
Ideal storage conditions are temperatures between 65° and 75°, and a relative humidity of 30 to 40%.
-
Many manufacturing concerns will at least add humidity during the winter months to minimize the wood from excessively drying out. Adding moisture to the air during the winter heating months will also reduce the chances of end checking.
-
A few firms have decided that the much greater expense of dehumidification during the summer is worth it for at least the area where wood parts are stored. Strict control of the ambient temperature and humidity levels will eliminate the clamming problems for well dried wood.
-
The bending process and subsequent drying of the bend causes variations in the relative position of the ends to the net part. Therefore, untrimmed ends are not reliable to use for indexing in machining fixtures. We recommend that the first step in machining curves is to mark the ends with a marking gauge and trim bends to length before mounting in the fixture.
-
Restraining sticks screwed or stapled to the ends can help, but the bends will move in or out when the restraint is removed. Firms derive the most benefit from the restraint when most of the machining is performed before removing the stick.
There is an expanded explanation on the subject of water and wood in Section 3: Water and Wood of this website. To the woodworker, the impact of moisture on wood cannot be overstated.
Bending by letter
We use some of the letters in the alphabet to distinguish between the various curved shapes. Some of them resemble graphically the letters themselves, while others are the first letter of the word that describes the shape or the process used.
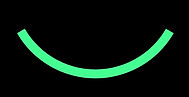
Radius bends: these bends are symetrical, with constant curvature which is the length of the inside radius. Table rims for round tables and sometimes chair parts are radii. For a refresher on what is a radius and circle geometry see section 2.2 Circle geometry refresher.
Clamming: Smaller radii will move more; as radii get larger 40 R, the tendency becomes only to flatten out; longer lengths move more.
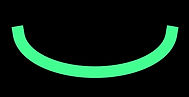
C shaped bends are symetrical, but are not a true radius. Geometrically they are a section of an elipse. These are found in top rails to chairs, and make a section of an eliptical table.
Clamming: Smaller curves will move more; as the curve get flatter, the tendency becomes only to flatten out; longer lengths more.

Eliptical shaped bends are not symetrical, and do not have straight ends. This shape can be a chair arm or leg; they can also form ¼ of an eliptical table.
Clamming: This shape curve is more cooperative in that if your machining operation permits moving the net part to the left (in the picture) if the ends move apart, and to the right if they move together.

J shaped bends are straight on one end, and have a hook on the other end.
Clamming: This shape curve is even more cooperative in that less of the wood is bent so there is less movement. If your machining operation permits, moving the net part to the left (in the picture) if the ends move apart, and to the right if they move together.
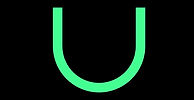
U shaped bends, like the letter U, have straight ends, and a curve in the middle. The curve can be as much as 180ْ of the circle. Seat rails and top rails that extend into arms are examples. When the angle of the curve is greater than 180ْ the parts want to “lock” onto the die.
Clamming: This shape curve is prone to the greatest amount of movement. These bends are usually long in length, have a large amount of curved wood and any movement will take it right out of spec.

V shaped bends, like the letter V, have two straight ends, and a bend between them. The two straight ends may or may not be the same length.
Clamming: If this shaped curve has long straight ends, and a sharp curve, then there is likely to be movement.

W bends. OK, it does not resemble the letter W, but consists of two V or J shapes. The middle may be more or less straight. Settee benches are one example of this bend. This is one of the more difficult bends to get a consitant curve from one bend to another, and will require more development to get it right than other curves. The challenge with this bend is that the section between the curves shrink different amounts.
Clamming: Movement of this shaped curve is complex. Two different curves double the opportunity for variations. The section between the curves behaves differently from bending to bending after drying. There is a tendency for the straight section to pick up the some of the adjoining curves. Extra material in the C dimension (our thickness dimension) helps to accommodate variations.

S shaped bends resemble the letter S. We have seen them as chair arms and back posts. We do not manufacture bends of this shape. The tooling and the press are very special and are specific to each shape.
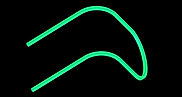
H, we use the letter “H” to refers to bends that are usually executed by hand, rather than by machine. An example of an H shaped bend is a continuous arm windsor bend, which involves bending in two planes. The tooling to execute these bends by machine is very specific, and unless the volumes are large, cannot be financially justified. We do not do hand bends.
Snaking
We use the term snaking to describe undesirable lateral movement in the bending blank that occurs during bending. This part movement cannot be removed after it occurs. Grain run-out, irregular grain, and too much steam, all exacerbate this tendency. As the C dimension increases (part thickness) beyond the B dimension (part width) snaking occurs more frequently; we call this bending the hard way. It is possible to bend parts the hard way depending on a multitude of factors; we welcome the opportunity to discuss parts that require this type of bend with you. Please see the section on re-sawing as this may be a good option.

Bending taller than wide or bending the hard way
If the C dimension (part thickness) is greater than the B dimension (part width), we call this bending the hard way. Bending the hard way is prone to induce undesirable snaking. We are usually able to work around this by bending a wide bending blank so that the B dimension is greater than the C dimension. After the blank is bent and
stabilized we rip the blank to the specified B dimension on a band saw. The shape of the bend determines whether it is suitable for re-sawing; there are bend shapes and sizes that we are unable to re-saw; very large hoop bends are difficult to re-saw.

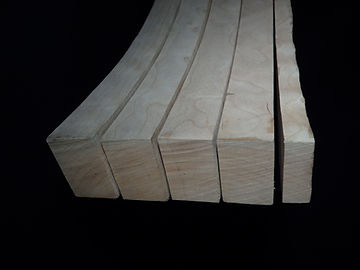
Rippling
The rippling shown on this 8/4 cherry bend is not a defect, but
occurs during bending as the wood cells rearrange during bending. Rippling can be either concave or convex; there is no way to tell which way it will go until the part is bent. The amount of rippling varies from minimal to quite significant depending on how tight a curve and how thick the part is. This is one of the reasons that we do not recommend trying to bend parts to net size and shape. We typically recommend 1/8” or more stock allowance per side beyond your net part size. Other factors that affect how much stock allowance to leave are: the part thickness, overall part size, and the shape of the bend. A thick part will usually have more rippling than a thinner part. This is why bending a net sized, or pre-machined part is not usually feasible.
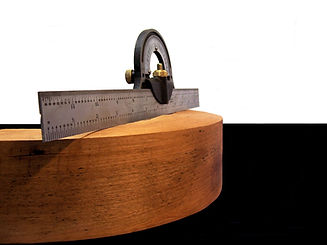
Compression
Not only does the inside length of the wood compress shorter, but the thickness also compresses thinner. The tighter the curve, the more the wood will compress. This example of 10/4 walnut bent more than 90° compressed from 2-3/8” to 1-1/4” at the center of the bend. At the bend, the wood will be much denser than average. This is not a bending failure, and will have to be taken into consideration when designing bent wood parts. Increasing the thickness of the bending blank to allow for the net part to be encapsulated inside the blank only works up to a point; eventually the point is reached where the cells have completely compressed and then the bending forces exceed the strength of the wood.

Folding
When all the bending stresses become concentrated in one area folding can occur. Unless the folding is minor, these are culled out prior to shipping. Any species can fold during bending for any number of reasons. Both under and over steaming can increase the chances of folding. Woods that are softer, have lower strength, or have a lower specific gravity are more likely to have issues with folding. The wider the annual growth rings are, the weaker the wood is, making it more likely to fold or break.

Feathering
Feathering is a bending term to describe very shallow lengthwise or longitudinal grain separation.

Pin knots
Pin knots in lumber are the fossils of a tree branch that got started, but never developed into a full branch. Pin knots occur in all species, but cherry is notable for frequent occurrences. Walnut and soft maple have their share of pin knots. Pin knots are too prevalent to cut out of every bending blank, but do remain problematic to bending. When they fail in the bending process, they often open up a diamond shaped void in the bending blank, this blank is then scrapped.

Why don’t most tropical woods bend very well?
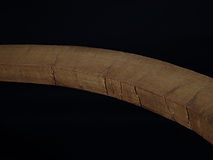
We have never read a good explanation to this question. 35 years of steam bending does suggest that the most likely reason is that tropical woods do not have annual growth rings in the same way that species from temperate forests do. Tropical species do not have seasons of growth. In temperate climes, there is a burst of growth in the spring that slows down during the hotter, dryer, summer. Visually, we view these transitions as growth rings. The later growth is denser and stronger than the earlier growth. This is especially true in the ring porous woods like oak and ash. Ring porous woods are the best bending of all the species. Mahogany does change the direction of its cells in an alternating corkscrew pattern, but there is not a change in the strength of the wood. When the stresses of bending are applied, they all get concentrated on the first weak spot forming a catastrophic failure. When steam bending temperate species, these stresses can be distributed more evenly with early growth doing most of the compression; the stronger later growth holds it together and distributes the compression lengthwise along the grain.
Too tight to bend
There is a physical limitation to how close our bending machines can bend a piece of wood. Our bending machines have a heavy steel framework to withstand the extreme forces required to bend the wood into the specified curve. As curves get tighter, eventually this framework will come around and meet.
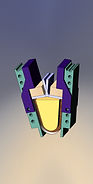
Water and Wood
Wood technologist Bruce Hoadly , explains the relationship between wood and water very well in his book: Understanding Wood: A craftsman’s guide to wood technology. Bruce estimates that 90% of all problems with wood involve moisture. Looking closely at Individual wood cells, they are about 1/1000 of an inch in diameter, and 1/10 inch long. The cell walls have a specific gravity of about 1.5, and are hollow like straws. Water is present both inside the cells as well as bound in the cell walls. The total water bound up in the wood is referred to as the moisture content (MC), which is expressed, as a percentage. This is measured as the ratio of the weight of water in a given piece of wood to the weight of the wood when it is completely dry. Freshly cut walnut can have a MC as high as 90%. Moisture begins to evaporate out of the wood as soon as the tree is cut, unless it is submerged in water. When the moisture content of wood is above 28%, it still has water inside the hollow cells; this water is called free moisture. As the free moisture is lost, the wood shrinks very little. For most species, when wood is dried below 28% moisture content, the free water is gone and the cell walls start drying out. As the cell walls dry out, they shrink in size. Eventually, if the humidity level is constant, and the wood is not losing or gaining moisture, the wood is said to be at the Equilibrium Moisture Content (EMC). The average EMC for wood in an indoor environment for much of the United States is 6 ½ %. To get the wood to this target MC, the wood must be dried, most likely in a kiln.
Drying
Dimensional Shrinkage
How much wood shrinks varies considerably among species. Making
drying even more complex, wood shrinks different amounts
depending on the orientation of the grain. A sponge is isotropic
meaning that as it dries it shrinks uniformly; wood is anisotropic,
meaning that it shrinks differently along each of its three grain
orientations.
-
Lengthwise shrinkage is between 0.1% and 0.2% for most
species. This is about 1/16” over 8’; in most cases, this small
amount of movement is generally ignored. -
Radial shrinkage, between the bark and the center of the tree
(pith), typically falls between 3% and 5%. -
Tangential shrinkage, along the annual growth rings, typically
falls between 6% and 10%.
The percentage difference between the radial shrinkage and the tangential shrinkage explains how cupping, diamonds, and other shapes occur during drying. The picture above graphically shows the relative shrinkage for how and where the board is cut from the log. The section on species gives the average shrinkage values for each of the species we bend. As you might expect, woods that have larger shrinkage values are more challenging to dry than those with smaller shrinkage values.
-
Volumetric shrinkage is the sum of radial, tangential, and longitudinal shrinkage. It ranges from 9% to15% for most species.
-
The tangential shrinkage to radial shrinkage ratio indicates the uniformity of the shrinkage with 1 being ideal or isotropic, and stable. Walnut is exceptionally stable for wood, with a ratio of 1.4; most of the species we bend have a ratio around 2.
Understanding why and how the wood moves is essential to working with it. The only time wood changes dimensionally is when the moisture content changes; temperature change has no dimensional effect on the wood. Wood has the property of being hygroscopic meaning that it acts similar to a sponge either gaining or losing moisture to the air relative to the humidity of the air. The finishes put on wood can slow down this migration, but the wood will always be reacting to any difference between its MC, and that of the moisture in the environment. What does kiln dried mean? Kiln dried is a term used in the wood working industry to describe wood that is between 6% and 8% MC. This is the industry standard, and the moisture content specified by the National Hardwood Lumber Association (NHLA), as well as the Wood Component Manufacturer Association (WCMA) in order for it to be considered kiln dried. This 6% to 8% MC is also optimum for wood stability in an indoor environment for most of the United States. There are EMC conditions that do fall outside of this average. Phoenix AZ can have EMC conditions of 4% while southern Florida can be in the mid teens. But for most areas of the country, an EMC of 6-8% is a workable average. If the MC of wood is higher than 8%, then the wood will shrink and change dimension. This can lead to joints opening, or even failing. Glues and finishes are formulated to work best at the kiln dried moisture content. Wood that is too dry will be difficult to machine, and will also negatively affect gluing and finishing.
Bending wood introduces additional stress along the length of the piece. When a blank of wood is bent, there is only a 1-2% increase in length. Bending wood largely consists of compressing the wood cells lengthwise by folding them up like an accordion. The cell compression will be greatest at the inside center of the bend, and less at the outside of the bend. On sharper bends, the wood will compress substantially in thickness (C dimension). The lengthwise cell compression also extends beyond the confines of the bend. In the final drying, these compressed cells continue to shrink lengthwise changing the shape of the curve. We compensate for most of this movement prior to drying by adjusting the shape of the bending die. We fine tune the final shape of the part after drying to meet specifications before shipping. Even after the part has been dried to the required 6% to 8% MC the part will move as the moisture content changes. You would observe this as the curve becoming tighter in very dry conditions when the heat is on in the middle of the winter; or conversely, the curve relaxing, or opening during very humid wet conditions during the summer.

Surface Checking, End Checking, and Honey Comb
Wood shrinks as it dries; and if the board does not dry evenly, with the outside of the board shrinking faster than the inside, stresses are created in the board. If the cells on the inside of the board are stronger than those on the surface of the board, a lengthwise split or surface check will occur. If the cells on the outside surface of the board are stronger; the cells on the inside of the board will collapse and leave a void called a honeycomb. The centers of the cathedrals in flat sawn lumber are the most susceptible to surface checking. Notice that the surface checks on the white oak board are confined to the cathedrals.

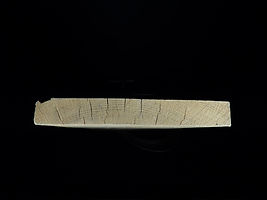

Color issues
Brown, orange, and gray staining in wood
During hot humid weather, wood is susceptible to changing in color. This is an oxidation process analogous to the rusting of iron. The color is gray in soft maple, and orange in hard maple. Very slow drying species like white oak, American beech, and hickory often leave a “shadow” from where the stickers were laid. Staining (color change) can happen in the log before it is sawn, or in the board after it has been sawn. Staining is not usually a problem with dark colored species like walnut or cherry. White woods like hard and soft maple are the main concerns. We work with sawmills that understand this, and we build up our inventory of the white woods during the winter when drying conditions are more favorable. Lumber that is frozen is much less susceptible to staining.

Blue Iron stain
All hardwoods contain varying amounts of tannic acid with the oaks having some of the highest percentages. This is the same acid that gives tea and red wine their astringent bite. When tannic acid comes into contact with iron, it rapidly oxidizes the iron forming iron tannate, and leaves a dark blue stain anywhere the iron contacts the wood. Trace amounts of iron picked up in the steel steam pipe is enough to pepper the wood with blue dots. Unless the contact with iron is prolonged, most of the stain can be readily removed with oxalic acid. Oxalic acid is sold at hardware stores as “Wood bleach”. It is an acid, and must be handled safely. This includes eye protection, and rubber gloves. Read and follow the instructions on the container.
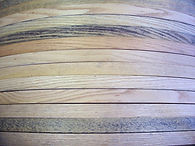

Scientific and Industry Terms
Modulus of Rupture, Elasticity, and Compression
A modulus is a number indicating the degree to which a species possesses that property. By itself, it is not very meaningful, but it is useful to woodworkers in making comparisons between species. If one has worked with silver maple, and wondered how much different red maple would be to work with, a comparison of the values will at least partially answer that question.
Modulus of Rupture (MOR) is a measure of the beam strength; the force that can be applied to the center of a beam that is only supported at its ends before it breaks. The units are in pounds force per square inch (lbf/in²), or Megapaschals (MPa). This is the best overall indication of the relative strength of a species.
Modulus of Elasticity (MOE) measures the wood’s resistance to breaking; how far the wood can be flexed and return back to its original shape when a force is applied to the end of it. Some species will bend considerably, but do not break easily. This is an indication of whether a species will be stiff or springy in an application compared to a different species. The following illustration compares the MOR and MOE of cherry and tulip poplar.

Table 1 at left, compares cherry and tulip poplar. Cherry has more ultimate strength (MOR) but is more flexible (MOE) than Tulip Poplar. If we compare two beams (boards of identical length width and thickness) made from each species we can infer the following. The cherry beam will deflect more than the tulip poplar beam when the same amount of weight is applied. The cherry beam will support more weight than the tulip poplar beam before it fails catastrophically. However, in reality these values are averages for each species, and individual samples could have these values reversed.
Modulus of Compression (MOC) is a measure of the compression strength parallel to the grain. This number is useful when using wood as a post, rather than its suitability as a beam which is the measure of the MOR.
Are these numbers useful in predicting how well a species will steam bend?
Low overall strength numbers can accurately predict that a species will not bend well, but, simply having higher strength numbers does not guarantee success. Mahogany, a tropical species, does not bend well at all, yet the strength of the material is quite high.
Janka Hardness
Janka hardness is the pounds-force, or newtons required to press a .444” (11.28 mm) diameter steel ball halfway into a species of wood. It is useful to the woodworker to predict how well that species will wear in service. Species with higher numbers will not dent as easily as a species with a lower number.

What are the differences between rift sawn,
quarter sawn, and flat or plain sawn lumber?
The top bend is flat sawn; the next one down is rift sawn; the bottom bend is quarter sawn. The difference between the three is how they are sawn out of the log. Flat sawn is the most common as it yields the most lumber from a log. The yield for rift and quartered sawn is about 15% less than that of flat sawn. Choosing how to have lumber is sawn can be aesthetic as well as practical. Quarter sawing yields the most fleck or flake (displays the medullary rays) especially in white oak. Flat sawn is generally preferred for bending; the others will bend, but with more compression and increased folding. Drying is slower for rift and quartered, but they are less susceptible to surface checking. Notice the end and surface checking on the top flat sawn bend.


Curly figure
The figure called curly occurs variously in all species, but is especially prevalent in both red and silver leaf maple. The degree of how curly a board is can vary between just perceptible to stunningly exaggerated. The wavy grain structure will increase the risk of bending failure due to folding, lengthwise grain separation, snaking, and breakage.
Brash wood
Wood is considered brash when there are fewer than six growth rings per inch, or incipient decay has set in. Brash wood is brittle and tends to crack or break when bent. Cherry has the highest occurrence of brash wood of the species that we bend.


Selected Species that Bend Well
White Ash
Common name(s): White ash, American white ash
Botanical name: Fraxinus americana
Specific gravity: 0.60
Average dried weight: 35 lbs/ft³; 560 kg/m³
Janka hardness: 1320 lbf; 4,230 N
Modulus of rupture: 15,000 lbf/in²; 84.8 MPa
Modulus of elasticity: 1,740,000 lbf/in²; 10.30 GPa
Crushing strength: 7410 lbf/in²; 49.0 MPa
Shrinkage:
-
Radial: 4.9%
-
Tangential: 7.8%
-
Volumetric: 13.3%
-
T/R Ratio: 1.6
Color: Sapwood is nearly white; heartwood is light brown; sometimes darker. Sapwood is often not clearly demarcated from heartwood.
Drying characteristics: This wood can turn light orange if not dried in a timely manner.
Grain structure: Ring-porous; similar to red oak; grain is usually straight.
Bending characteristics: Very Good
Comments: Good strength properties for its weight; shock resistant. It has been long used for baseball bats.

The emerald ash borer
In the 1990s an invasive species, the emerald ash borer (EAB) was introduced to North America from Asia. This beetle bores into the cambium layer of the tree (The cambium layer is the living cells of the tree between the bark and the wood) which effectively girdles and kills the ash tree. Once the tree is girdled, it quickly starts losing strength; industry has labeled this early decay as brash wood. When we bend brash or dead wood, it fractures. As of 6/1/2016, we have stopped purchasing ash due to the disproportionate amount of brash or dead wood received. We estimate that 80% of the last load of ash we received was brash or dead; we rejected the entire shipment. At this time we do not have a supplier that can guarantee they will provide wood from live trees. Once the ash we have in inventory is depleted we will no longer offer ash as a species that we will bend. The damage caused by the emerald ash borer will likely be similar to Chestnut blight and Dutch elm disease.

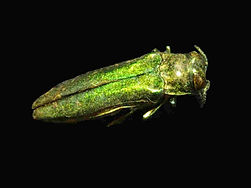

Cherry
Common name(s): Cherry, Black cherry, American cherry
Botanical name: Prunus serortina
Specific gravity: 0.56
Average dried weight: 44 lbs/ft³; 705 kg/m³
Janka Hardness: 950 lbf; 6,450 N
Modulus of Rupture: 12,300 lbf/in²; 84.8 MPa
Modulus of Elasticity: 1,490,000 lbf/in²; 10.30 GPa
Crushing Strength: 7,110 lbf/in²; 49.0 MPa
Shrinkage:
-
Radial: 3.7%
-
Tangential: 7.1%
-
Volumetric: 11.5%
-
T/R Ratio: 1.9
Color: Sapwood is a pale yellow; over time and exposure to light, the heartwood darkens to a golden brown.
Tendency to discolor during drying: This wood does not usually have any color change problems associated with drying.
Grain structure: Semi diffuse porous; grain structure is often irregular which can cause problems in bending.
Bending characteristics: Fair; it is softer than the other common cabinet species, and like other fruitwoods, has a higher rate of bending failures. Pin knots, resin/gum pockets, and grain run out are challenges.
Comments: A premium cabinet species since colonial times; prized for the rich reddish-brown patina it develops.

Hard maple
Common name(s): Hard maple, Sugar maple, Rock maple
Botanical name: Acer saacharum
Specific gravity: 0.63
Average dried weight: 44 lbs/ft³; 109 kg/m³
Janka Hardness: 1450 lbf; 6,450 N
Modulus of Rupture: 15,800 lbf/in²; 84.8 MPa
Modulus of Elasticity: 1,830,000 lbf/in²; 12.62 GPa
Crushing Strength: 7,830 lbf/in²; 54.0 MPa
Shrinkage:
-
Radial: 4.8%
-
Tangential: 9.9%
-
Volumetric: 14.7%
-
T/R Ratio: 2.1
Color: When winter cut, the sapwood is nearly white; heartwood is darker reddish-brown.
Tendency to discolor during drying: This wood can turn orange if not dried in a timely manner. The white color is easier to achieve when cut and dried during colder temperatures.
Grain structure: Diffuse porous with a very fine even texture, and is likely to Exhibit chatoyancy.
Bending characteristics: Good to very good, this is one of our favorite woods to bend.
Comments: The sapwood is preferred over the heartwood in this species. It is a premium cabinet maker species which occasionally has curly, or fiddle back figure. Even rarer is quilted and birdseye figure. This is the species that is usually tapped to make maple syrup. This wood has found a following with major league baseball players, many of them have their bats made from hard maple.
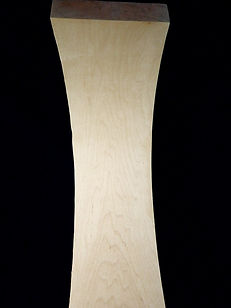
Red maple
Common name(s): Red maple
Botanical name: Acer rubrum
Specific gravity: 0.54
Average dried weight: 38 lbs/ft³; 610 kg/m³
Janka Hardness: 950 lbf; 4,230 N
Modulus of Rupture: 13,400 lbf/in²; 92.4 MPa
Modulus of Elasticity: 1,640,000 lbf/in²; 11.31 GPa
Crushing Strength: 6,540 lbf/in²; 45.1 MPa
Shrinkage:
-
Radial: 4.0%
-
Tangential: 8.2%
-
Volumetric: 12.6%
-
T/R Ratio: 2.1
Color: Sapwood is light golden; heartwood is brown sometimes with an olive green cast.
Tendency to discolor during drying: This wood is very susceptible to gray staining when sawn and dried during warm temperatures. Other than the color issue this wood is very easy to dry
Grain structure: Diffuse porous with a very fine texture.
Bending characteristics: Good
Comments: Red and silver maple are sold commercially as soft maple with no distinction between them. Soft maple often contains a percentage of curly and quilted figure.
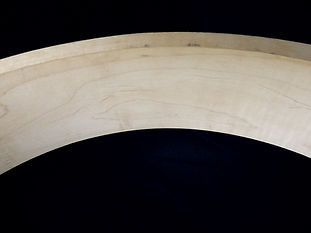
Silver maple
Common name(s): Silver maple
Botanical name: Acer saacharinum
Specific gravity: 0.47
Average dried weight: 33 lbs/ft³; 530 kg/m³
Janka Hardness: 700 lbf; 3,110 N
Modulus of Rupture: 8,900 lbf/in²; 61.4 MPa
Modulus of Elasticity: 1,140,000 lbf/in²; 7.86 GPa
Crushing Strength: 5,220 lbf/in²; 36.0 MPa
Shrinkage:
-
Radial: 3.0%
-
Tangential: 7.2%
-
Volumetric: 12.0%
-
T/R Ratio: 2.4
Color: Sapwood is quite white; heartwood is brown sometimes with an olive green cast.
Tendency to discolor during drying: This wood is very susceptible to gray staining when sawn and dried during warm temperatures. If color is not a concern this is a very easy wood to dry.
Grain structure: Diffuse porous with a very fine texture. It can have irregular grain.
Bending characteristics: Fair; low strength characteristics limit it’s suitability for steam bending
Comments: Red and silver maple are combined and sold commercially as soft maple. It often contains a percentage of curly and quilted figure.

What is the difference between hard, red, and silver maple?
Of the three, hard maple is the premium species; it has: the whitest color, straightest grain, and is also the strongest. Red maple is a northern species that resembles hard maple, but is manila colored and softer (but still quite hard), and not as strong. Silver maple’s range extends further south where it can be very fast growing. Whiter than its cousin red maple, it is the weakest, softest and least suitable for bending. Silver maple is sold in combination with red maple, and all of it is labeled as soft maple.
Poplar
Common name(s): Poplar, Tulip poplar, Yellow poplar
Botanical name: Liriodendron tulipfera
Specific gravity: 0.42
Average dried weight: 29 lbs/ft³; 550 kg/m³
Janka Hardness: 540 lbf; 2,400 N
Modulus of Rupture: 10,100 lbf/in²; 69.7 MPa
Modulus of Elasticity: 1,580,000 lbf/in²; 10.9 GPa
Crushing Strength: 5,540 lbf/in²; 438.2 MPa
Shrinkage:
-
Radial: 4.6%
-
Tangential: 8.2%
-
Volumetric: 12.7%
-
T/R Ratio: 1.8
Color: Sapwood is off white to light yellow; heartwood is light tan. The line between the two is not always clearly demarcated. Mineral staining can leave colors ranging from black, dark purple, red, green and yellow.
Tendency to discolor during drying: Lumber grading rules do not grade against color in this species. If not dried promptly after sawing, it will stain. We do not sort this wood for color.
Grain structure: Diffuse-porous; grain is straight and uniform with few knots.
Bending characteristics: Fair; low strength characteristics limit it’s suitability for steam bending.
Comments: Yellow poplar is a very large, abundant, and fast growing tree. Although relatively light, it is strong for its weight, but it is not as strong as other hardwoods. It is straight grained and somewhat brittle. The lower overall strength limits how sharply this wood can be bent without breaking.

Red oak
Common name(s): Red oak, True northern red oak
Botanical name: Querus rubra
Specific gravity: 0.63
Average dried weight: 44 lbs/ft³; 700 kg/m³
Janka Hardness: 1,220 lbf; 5,430 N
Modulus of Rupture: 14,480 lbf/in²; 99.2 MPa
Modulus of Elasticity: 1,761,000 lbf/in²; 12.14 GPa
Crushing Strength: 6,780 lbf/in²; 46.8 MPa
Shrinkage:
-
Radial: 4.0%
-
Tangential: 8.6%
-
Volumetric: 13.7%
-
T/R Ratio: 2.2
Color: Sapwood is white to light brown; usually quite narrow; heartwood is light tan, sometimes with a reddish-pink cast.
Tendency to discolor during drying: Not usually a problem. Sticker shadow can be an issue due to the high initial moisture content. Using dry stickers will help mitigate sticker shadow.
Grain structure: Ring porous with a course, uneven texture. The grain is normally quite straight.
Bending characteristics: Excellent; it is one of the best bending species. Ring porous species will compress more than diffuse-porous species.
Comments: Red oak is the commercial term for a group of 17 closely related species. The True Northern red oak is the premium species of the lot, and also offers the best color and drying characteristics out of the other species of oak. Northern red oak is the species that we use exclusively.

Walnut
Common name(s): Walnut, Black walnut
Botanical name: Juglans nigra
Specific gravity: 0.55
Average dried weight: 38 lbs/ft³; 610 kg/m³
Janka Hardness: 1,010 lbf; 4,490 N
Modulus of Rupture: 14,600 lbf/in²; 100.7 MPa
Modulus of Elasticity: 1,680,000 lbf/in²; 11.59 GPa
Crushing Strength: 7,580 lbf/in²; 52.3 MPa
Shrinkage:
-
Radial: 5.5%
-
Tangential: 7.8%
-
Volumetric: 12.8%
-
T/R Ratio: 1.4
Color: Sapwood ranges from nearly white to a pale yellow-gray; heartwood ranges from light brown to dark brown; sometimes with a dark blue or purple cast.
Tendency to discolor during drying: This wood doe not normally change color during drying. The longer the boards sit before drying does soften the definition line between the hart wood and the sap wood. The color from the heart wood bleeds into the sapwood a bit. Many places will steam the wood after it is dried to help color the sap wood to match the heart wood. We do not steam our wood during the drying process. This wood does however take more time to dry than some of the other species that we have.
Grain structure: Semi-ring porous with a moderate texture. Irregular grain, is common to fruitwoods, the irregular grain can be a problem in bending. Walnut has a tendency to have pin knots; we cannot cut all of them out.
Bending characteristics: Good
Comments: Good dimensional stability, shock resistance, and strength properties have made walnut a premium choice of furniture makers for centuries.
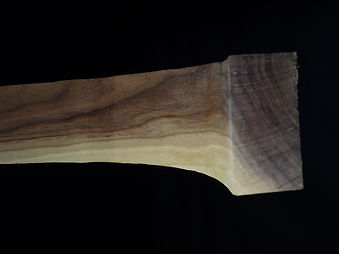
Selected Species that Are Difficult to Dry Without Degrade
White oak
Common name(s): White oak
Botanical name: Querus alba
Specific gravity: 0.67
Average dried weight: 47 lbs/ft³; 755 kg/m³
Janka Hardness: 1,350 lbf; 5,990 N
Modulus of Rupture: 14,830 lbf/in²; 102.3 MPa
Modulus of Elasticity: 1,762,000 lbf/in²; 12.15 GPa
Crushing Strength: 7,370 lbf/in²; 50.8 MPa
Shrinkage:
-
Radial: 5.6%
-
Tangential: 10.5%
-
Volumetric: 16.3%
-
T/R Ratio: 1.9
Color: Sapwood is white to light brown; the band of sapwood is usually quite narrow; heartwood is light brown, sometimes with a gray cast to it.
Tendency to discolor during drying: Drying is problematic; because of the high initial moisture content, dry stickers must be used to mitigate sticker shadow. Surface checking is difficult to avoid.
Grain structure: Ring porous with a course, uneven texture.
Bending characteristics: Excellent; it is one of the best bending species. Ring porous species will compress more than diffuse-porous species.
Comments: White oak is the commercial term for a group of 18 closely related species. Like its close cousin red oak, white oak is an excellent bending wood, but it is extremely difficult to dry without getting surface checking. A major cause for surface checking is by re-wetting the wood during the steaming process and the subsequent re-drying after it has been bent. Quartered lumber reduces the amount of surface checking; however the edges of the part are now vulnerable. Large, prominent medullary rays (commonly called flake or fleck) are prone to peel off during bending. Rift cut lumber is the best choice if white oak must be used.
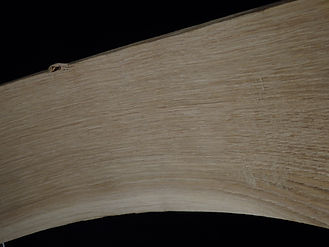
What is the difference between red and white oak?
These two closely related species have minor visual differences, but have significant differences at a cellular level. Their annual growth ring cell structure consists of alternating bands of very large open cell early growth, and very dense, strong, late growth. Red oak is manila colored with hints of red, and white oak is silvery gray. One other visual difference is the size of medullary rays. Wood rays are only prominent in true quartered lumber. In white oak, these rays can be the size of your palm. These wood cells are very dense and will likely peel off during bending.
The cellular level is where the real differences lie. Red oak cells are largely open and do not hold water. White oak cells are plugged with membranous tyloses. These make the wood largely impervious to water and the species of choice for bourbon barrels. The impenetrability to water of the white oak makes drying very slow and difficult without significant degrade. The steaming, bending, and subsequent re-drying greatly exacerbates the inherent tendency to surface check.
European beech
Common name(s): European beech
Botanical name: Fagus sylvatica
Specific gravity: 0.63
Average dried weight: 44 lbs/ft³; 710 kg/m³
Janka Hardness: 1,450 lbf; 6,460 N
Modulus of Rupture: 15,970 lbf/in²; 110.1 MPa
Modulus of Elasticity: 2,075,000 lbf/in²; 14.31 GPa
Crushing Strength: 8,270 lbf/in²; 57.0 MPa
Shrinkage:
-
Radial: 5.7%
-
Tangential: 11.6%
-
Volumetric: 17.3%
-
T/R Ratio: 2.0
Color: This species is often steamed to even out color variations. The steaming darkens the color from pale cream to brown.
Grain structure: Semi-ring-porous with a fine to medium texture.
Bending characteristics: Excellent; it is one of the best bending species.
Comments: European beech is one of the best bending species of all. However, in order for it to be imported into the United States, the USDA stipulates that it must essentially be kiln dried to kill off any invasive species concealed within. Our experience with bending this species indicates a high variability in the quality of the drying done overseas. The damage incurred in drying cannot be reversed, and will only get worse going through the steam bending process. The unreliability of the drying discourages us from offering this species for bending. American beach is an inferior species to European beech. It is an extremely slow drying species, and very prone to surface checking and discoloration.

Hickory
Common name(s): Mockernut Hickory
Botanical name: Carya tomentosa
Specific gravity: 0.75
Average dried weight: 51 lbs/ft³; 815 kg/m³
Janka Hardness: 1,970 lbf; 8,760 N
Modulus of Rupture: 19,200 lbf/in²; 132.4 MPa
Modulus of Elasticity: 2,220,000 lbf/in²; 15.31 GPa
Crushing Strength: 8,940 lbf/in²; 61.7 MPa
Shrinkage:
-
Radial: 7.7%
-
Tangential: 11.0%
-
Volumetric: 17.8%
-
T/R Ratio: 1.4
Color: Sapwood is a pale yellow brown; the band of sapwood is usually quite narrow; heartwood is light to medium brown.
Tendency to discolor during drying: Drying must be done with care; there is a tendency for surface checking and twisting.
Grain structure: Ring porous with a course, uneven texture.
Bending characteristics: Excellent; it is one of the best bending species. Considerable force is needed to bend this very tough, heavy species. Hickory is more commonly used for tool handles given its superior shock and overall strength properties, and is not commonly used for furniture. A lack of long clear cuttings limits its usefulness in steam bending.
Comments: Hickory is the commercial term for a group of 18 closely related species. There are two broad groups of hickory: true hickories, and pecan hickory. They are all similar in appearance, but their properties do differ. The properties given above are for mockernut hickory which is the hardest and heaviest of the group. Mockernut hickory has been long used for tool handles for its superior strength and shock resistance. It has recently found favor for use in kitchen cabinets and flooring where the defects are featured as a rustic look.

Selected Species that Do Not Bend Well
Mahogany
Common name(s): Honduran Mahogany, Genuine Mahogany, American Mahogany
Botanical name: Swietenia macrophylla
Specific gravity: 0.60
Average dried weight: 41 lbs/ft³; 655 kg/m³
Janka Hardness: 900 lbf; 4,000 N
Modulus of Rupture: 11,660 lbf/in²; 80.4 MPa
Modulus of Elasticity: 1,386,000 lbf/in²; 9.56 GPa
Crushing Strength: 6,550 lbf/in²; 45.2 MPa
Shrinkage:
-
Radial: 3.0%
-
Tangential: 7.8%
-
Volumetric: 7.8%
-
T/R Ratio: 1.4
Color: The color varies from pale pinkish brown to dark reddish brown which tends to darken over time.
Grain structure: Diffuse-porous with medium to large pores. The grain can be straight, but is often interlocked or wavy.
Bending characteristics: Only acceptable for the flattest bends, otherwise not at all.
Comments: There are a number of woods that go by the name of Mahogany, but Genuine Mahogany is the premier species. It is noted for its exceptional stability and easy workability.
Except for very flat bends, tropical woods do not bend well. They tend to kink and form creases that are objectionable when a finish is applied. The creases are denser than the surrounding wood and do not accept stain in the same way; the result is that after staining, they are lighter in color than the surrounding mahogany. We have yet to hear anyone characterize these marks as a design feature.

Bamboo
Common name(s): Bamboo
Botanical name: there are hundreds of species in dozens of genera from the Poaceae (grass) family.
Specific gravity: 0.50 to 0.85
Average dried weight: 31 lbf; 500 N to 53 lbf; 850 N
Janka Hardness: 1,410 lbf; 6,270 N to 1,610 lbf; 7,170 N
Modulus of Rupture: 11,020 lbf/in²; 76.0 MPa to 24,450 lbf/in²; 168.6 MPa
Modulus of Elasticity: 2,610,000 lbf/in²; 18.00 GPa to 2,900,000 lbf/in²; 20.00 GPa
Crushing Strength: 8,990 lbf/in²; 62.0 MPa to 13,490 lbf/in²; 93.0 MPa
Shrinkage: Diameter: 10-16%; wall thickness: 15-17% Bamboo shrinks more than oak.
Color: Yellow to white.
Tendency to discolor during drying: Bamboo that is not harvested in a timely manner can develop fungal decay which will leave brownish black streaks.
Grain structure: Bamboo does not have annual growth rings; it is a monocot in the grass family. Bamboo is hollow, and when it is processed into lumber it is first split, and then edge glued into a wide piece. These can be further laminated to make a thicker panel. There will be some variation in appearance where nodes appear in the stem.
Bending characteristics: Since bamboo lumber is plied together similarly to plywood, it does not lend itself to bending at all.
Comments: Bamboo has been used as a building material for 5,000 years. China grows and processes almost all of the bamboo available commercially worldwide. Bamboo is the common term for hundreds of species. A natural bamboo forest reaches maturity in about 8 years. Cultivated bamboo, with abundant rainfall or irrigation, and fertilization, matures in as little as 2-3 years. This extremely short growing cycle has given it a very high green reputation. To meet the increase in worldwide demand, indigenous forests are being cut down and made into bamboo monoculture plantations. A tremendous amount of biodiversity is lost. Besides fertilizers, pesticides are also applied. Naturally managed hardwood forests are neither fertilized nor do they use pesticides. Bamboo is hollow. To be useful it must be cut into strips and glued together. As much as 15% of the board weight is the glue used to hold it all together. These glues are often oil based, and may or may not be environmentally friendly; the Chinese are very good at using the least expensive, readily available material. For additional reading on this remarkable plant, Dovetail Partners has published an excellent study of the benefits and environmental cost of bamboo. www.dovetailinc.org/report_pdfs/2014/dovetailbamboo314.pdf
Red alder
Common name(s): Red Alder, Western Red Alder
Botanical name: Alnus rubra
Specific gravity: 0.41
Average dried weight: 28 lbs/ft³; 450 kg/m³
Janka Hardness: 590 lbf; 2,620 N
Modulus of Rupture: 9,800 lbf/in²; 67.6 MPa
Modulus of Elasticity: 1,380,000 lbf/in²; 9.52 GPa
Crushing Strength: 5,820 lbf/in²; 40.1 MPa
Shrinkage:
-
Radial: 4.4%
-
Tangential: 7.3%
-
Volumetric: 12.6%
-
T/R Ratio: 1.7
Color: The color varies from almost white to pale pinkish brown. Sapwood and heartwood are not demarcated.
Grain structure: Diffuse-porous with a moderately fine, uniform texture.
Bending characteristics: Poor; very low strength characteristics, and yielding only small cuttings limit it’s suitability for steam bending
Comments: Red alder is a member of the birch family and grows on the Pacific coast. It is only recently that red alder has been sawn for grade. For years this species was only harvested for firewood. It now has a following in rustic applications. Even the best cuttings are short, and contain significant grain run out, irregular grain, and knots. That, along with a low specific gravity, makes this wood a poor candidate for steam bending.

Teak
Common name(s): Teak, Burmese Teak
Botanical name: Tectona grandis
Specific gravity: 0.55
Average dried weight: 41 lbs/ft³; 655 kg/m³
Janka Hardness: 1,070 lbf; 4,740 N
Modulus of Rupture: 14,080 lbf/in²; 97.1 MPa
Modulus of Elasticity: 1,781,000 lbf/in²; 12.28 GPa
Crushing Strength: 7,940 lbf/in²; 54.8 MPa
Shrinkage:
-
Radial: 2.6%
-
Tangential: 5.3%
-
Volumetric: 7.2%
-
T/R Ratio: 2.0
Color: Teak is a golden or medium brown.
Grain structure: Ring porous to semi-ring porous.
Bending characteristics: We have successfully bent teak on shallow bends where the inside did not show. As the curve gets sharper, teak tends to fold up like other tropical woods.
Comments: Long noted for its exceptional decay resistance, teak is used in marine environments, and outdoor furniture. Much of the teak today is plantation grown.

Lyptus®
Common name(s): Lyptus®, a trade name.
Botanical name: Eucalyptus urograndis x E. urophylla hybrid
Specific gravity: 0.72
Average dried weight: 53 lbs/ft³; 850 kg/m³
Janka Hardness: 1,420 lbf; 6,330 N
Modulus of Rupture: 17,110 lbf/in²; 118.0 MPa
Modulus of Elasticity: 2,049,000 lbf/in²; 14.13 GPa
Crushing Strength: 8,640 lbf/in²; 59.6 MPa
Shrinkage:
-
Radial: 8.2%
-
Tangential: 12.8%
-
Volumetric: 21.0%
-
T/R Ratio: 1.6
Color: The color ranges from salmon to a brownish red.
Grain structure: Diffuse-porous with a medium texture. Lyptus® is plantation grown; it is pruned yielding few knots and generally straight grain.
Bending characteristics: Poor; behaves like other tropical woods
Comments: Lyptus is a plantation grown eucalyptus hybrid created by Weyerhaeuser that matures in 14-16 years. It is marketed as a cherry or mahogany substitute, and behaves in steam bending similar to other tropical species. The exceptionally high shrinkage values of this species will need to be accounted for. Except for very flat bends; tropical woods do not bend well. They tend to kink and form creases that are objectionable when a finish is applied. The creases are denser than the surrounding wood and do not accept stain in the same way; the result is that after staining, they are lighter in color than the surrounding wood.

Frequently asked questions
Q: Can steam bending be used as they are received, or do they need to be machined?
A: The bendings will at least need to be trimmed to length.
Q: After receipt of a purchase order, how soon can I expect delivery?
A: Upon receipt of order, lead time is usually 2-3 weeks for orders of fewer than 150 bends. Thick and wide parts can take much longer to dry. It simply takes longer to dry the thicker, wider material without degrade.
Q: What moisture content is the part when it is shipped?
A: We dry bends to 6-8% moisture content as specified by the Wood Component Manufacturers Association.
Q: What species of wood does Michigan Chair Company inventory?
A: We inventory the following raw material:
-
4/4 to 10/4 Hard and soft maple, cherry, and walnut.
-
4/4 to 8/4 red oak, and as long as we can get it, ash.
-
6/4 yellow poplar (tulipwood)
Q: How many bends do I have to order?
A: You may order as few as one. If you have a small project, we usually give you a flat quote for that project. The flat quote will include your part(s), a bending die, patterns/gages, as well as bend development. A set up charge is assessed on small orders.
Q: How sharp a radius can Michigan Chair bend?
A: When bending wood to a radius smaller than three inches, there are a number of questions that must be answered, please contact us to discuss them.
-
What species of wood are we bending?
-
Where is the bend located in the bending blank?
-
What is the ratio of the B (part width) and C (part thickness)?
-
What is the thickness of the bending blank?
-
Wood begins to compress in thickness, will the customer be able to machine the net part out of the supplied bending blank?
-
Steam bending is seldom enjoys a 100% success rate. We have to cull out those that will not “clean up” after they are machined; what percentage of rejects do we expect?
-
How much will production need to be slowed to produce good bends?

Q: What is the thickest piece of wood we can bend?
A: We have a small amount of 3 inch thick (12/4) stock in cherry and walnut. We may be able to increase the C dimension beyond 3” if the bend is not too severe, and the B dimension (width) is less than 3”. We will have to bend your part the “hard” way, by ripping boards to the thickness of the bend (C dimension).
Q: Do some woods bend better than others?
A: We have the best results with the common, native American hard woods. There is little difference between ash, cherry, soft maple (red maple), red oak, and walnut. Hard maple (rock or sugar) bends well except at the smallest radii i.e. less than 2 inch radius for 2 inch thick stock.
Q: How long do the parts steam for?
A: Long enough so the bending blank is soft enough not to break on the outside, but not so long the wood becomes too soft and folds. Thin parts may steam for as short as 15 minutes, but thick wide parts bent to a sharp curve may need as long as 10 hours.
Q: What is the optimum moisture content for steam bending?
A: Wood at higher moisture content will steam much quicker, but wet wood is weaker than dryer wood. Wetter wood has more problems with collapse on the inside, separation on the outside of the bend, and hydraulic rupture. The steam time for wood below 10% moisture content is very long, and fractures on the outside of the bend are more likely. We bend our lumber in the mid teens.
Q: What lumber moisture content is recommended for gluing and machining?
A: The Wood Component Manufacturers Association specifies 6-8% moisture content as this is where lumber machines best. Glues and finishes are designed for this moisture content. Above 8% wood will continue to dry and move. We dry bends to 6-8% moisture content as specified by the Wood Component Manufacturers Association.
Q: What are the best storage conditions for my bends?
A: We recommend storing at: 65° F to 75° F with relative humidity at 35%. Do not store bends directly on a concrete floor where they can absorb moisture or where they would otherwise get wet. Do not store bends in proximity to hot air registers or radiators as they can continue to dry and change shape.
Q: Can my bends move over time?
A: When bends lose moisture, they tend to pull in or become more curved. When bends pick up moisture, they tend to flatten out. Large radius bends (very flat) tend to just flatten out.
Q: What can be done with parts that have flattened out?
A: If parts have lost some of their curve, a bar clamp or case clamp across the corners can be used to gently bring the part past the desired curve and then held there for several days usually works to bring the part into tolerance. If they have gained significant moisture, the part may need to be re-dried.
Q: What can be done with parts that have moved in?
A: One method of flattening out a bend is to place it concave down on a work bench aligned parallel with the over hang of the bench top. Use a bar clamp between the bottom of the bench top and the center of the point farthest away from the pattern to gently squeeze the bend a little past (for spring back), hold, release, and repeat if necessary.
Q: Does Michigan Chair Company use anhydrous ammonia in bending?
A: We do not use anhydrous ammonia. The University of Wisconsin pioneered the research in using anhydrous ammonia, and we thank Graham Burbank for the following information. Parts plasticized with anhydrous ammonia have the feel of hard rubber, can be bent in any direction, and may not need a support strap. Anhydrous ammonia is attracted to water, and will adhere to all mucus membranes, eyes, lungs, and skin. Anhydrous ammonia will stain hardwood black completely through, and it takes from 1 to 3 weeks for the ammonia to off gas out of the part. Anhydrous Ammonia is extremely poisonous, federally regulated, and environmentally unfriendly. Using steam bending is just as effective, safer, and less expensive than using anhydrous ammonia.
Steam bending tips
If you wandered into this website looking for information on how to bend wood, this is your area. The following information is offered in response to some common questions. We do not answer personal questions.
The online tool maker and seller Veritas sells hand bending equipment including: steamers, bending straps, end blocks, and fixtures for changing bending directions. They also have an excellent manual available for free online which is written to help someone getting started. It is well worth reading. www.leevalley.com/US/htm/05F1501ie.pdf
Q: What material can be used for a support strap?
A: Any iron strap (i.e. banding) with end supports will help, but iron does leave black surface stain on the part. Painting the steel will help reduce this. Stainless steel will eliminate this problem.
Q: What is the optimum moisture content for steam bending?
A: Although wood with a moisture content above 25% will steam much quicker, it tends to have more problems with collapse on the inside and separation on the outside of the bend. The steam time for wood below 10% is very long, and fractures on the outside of the bend are more likely. We bend our lumber in the mid teens.
Q: Can kiln dried lumber be successfully bent?
A: Yes, with the following observations:The greatest single factor in the success of a bending is how well it was dried down from green. Any common defects like surface checking and honeycombing created in drying will only be magnified by steam bending. Species that are difficult to dry are especially prone to have seasoning defects. Bending wood that has been kiln dried at a maximum temperature of 140°F will have a much better success rate than trying to bend wood that has been kiln dried at a temperatures of 180°F or more which makes the wood very brittle. Getting the wood hot enough during steaming is the most common obstacle woodworking enthusiasts encounter when bending drier wood. Steam times will be much longer than when bending stock with a moisture content in the teens. Most kiln dried lumber has had the lignin (the natural glue of the wood) already set, and will not bend as well as lumber dried to our proprietary schedules.
Expect better results when using commercially supplied kiln dried lumber with:
-
Bends flatter than a 21 inch radius
-
Stock thinner than 1 ¼ inches
Q: How long do the parts steam for?
A: Long enough so the part is soft enough not to break on the outside, but not so long the wood becomes too soft and folds. We have not found that the “1 hour per inch rule” to be a useful guide. Trial and error is the best guide. The following observations may help. Most of the steam bending setups we have observed do not have their steam chambers adequately insulated. The intent of steaming is to get the wood hot. This is accomplished much easier if the steam chamber is well insulated. Secondly, many beginners steam too timidly. You will have better results if you steam aggressively in a well insulated chamber.
Q: Is a support strap necessary for bending?
A: Shallow, flat bends can be successfully bent without a strap, but with a sharper radius, a strap will improve the chances of success.
Q: What moisture content is the lumber when it is bent?
A: We bend our lumber in the mid teens.
Q: Is breaking a persistent problem?
A: If there is one common problem for beginners, our observations are that the wood is not getting hot enough. Although wood can be over steamed, especially if it has high moisture content, usually the problem is trying to bend wood that is too cold.
-
Start with a well insulated tank
-
You will need a robust steam generator operating aggressively
-
Keep the distance from the steaming system to the bending setup to a minimum
-
Have all of your clamps ready, and practice all your moves before hand to make sure of the order. Once the wood comes out of the steam tank, the clock is ticking.
-
Bend smoothly without jerking.
-
Not every bend will be successful. Selecting stock that is straight grained and free of irregularities will enhance your chances of success.